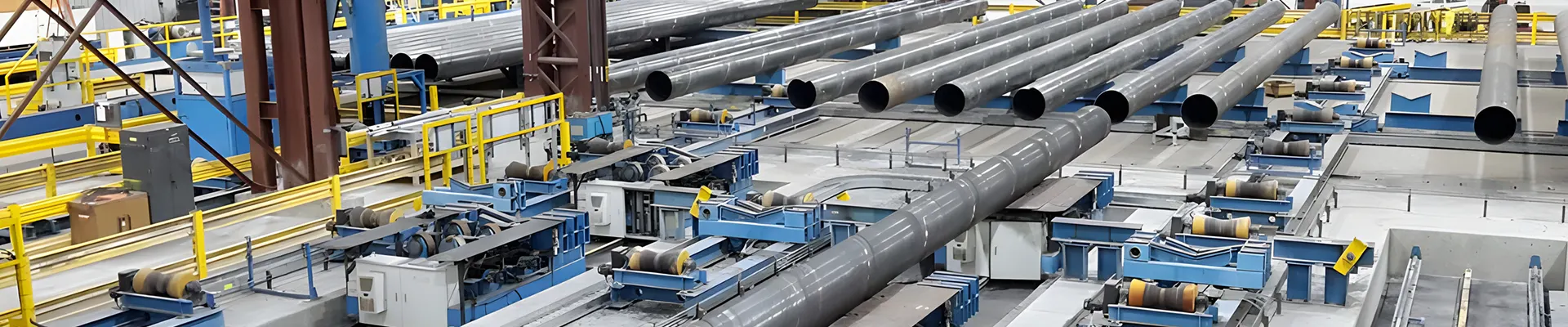
04
2025
-
07
Challenges in Working with S355 Welded Pipe and How to Overcome Them
Challenges in Working with S355 Welded Pipe and How to Overcome Them Table of Contents Introduction to S355 Welded Pipe Understanding S355 Steel Properties Common Challenges in Working with S355 Welded Pipe Welding Issues Corrosion Resistance Mechanical Properties Concerns Cost Implications Strategies to Overcome Ch
Author:
Challenges in Working with S355 Welded Pipe and How to Overcome Them
Table of Contents
- Introduction to S355 Welded Pipe
- Understanding S355 Steel Properties
- Common Challenges in Working with S355 Welded Pipe
- Strategies to Overcome Challenges
- Case Studies: Success in Utilizing S355 Welded Pipe
- Frequently Asked Questions
- Conclusion
Introduction to S355 Welded Pipe
S355 welded pipe is a popular choice in construction and engineering due to its remarkable strength, versatility, and cost-effectiveness. This structural steel is favored for various applications, including bridges, buildings, and other infrastructure projects. However, despite its benefits, working with S355 welded pipe does present several challenges that professionals in the field need to navigate. Understanding these challenges and developing effective strategies to overcome them is crucial for ensuring project success.
Understanding S355 Steel Properties
S355 is a structural steel grade that is known for its high strength and good weldability. It is part of the European standard EN 10025 and is designated as a low-carbon steel, making it suitable for various applications. The properties of S355 steel include:
- **Yield Strength**: Typically around 355 MPa
- **Ultimate Tensile Strength**: Approximately 470-630 MPa
- **Good Cold Forming Properties**: Allows for various shaping methods
- **Excellent Weldability**: Enables easy joining with other materials
These properties make S355 welded pipe an ideal choice for demanding applications. However, they also introduce specific challenges that must be addressed during construction and fabrication.
Common Challenges in Working with S355 Welded Pipe
Welding Issues
Welding S355 steel can present unique challenges due to its composition and properties. The primary welding issues include:
- **Preheat Requirements**: To prevent cracks during the welding process, preheating the material to a specific temperature is often necessary. Failing to do so can lead to defects in the weld joint.
- **Heat-Affected Zone (HAZ) Sensitivity**: The heat-affected zone can become brittle, compromising the integrity of the weld. Managing the welding parameters is essential to minimize these effects.
- **Distortion**: The process of welding can cause warping and distortion of the pipe, affecting the overall structural integrity.
Corrosion Resistance
S355 welded pipes, while strong, can be susceptible to corrosion, especially in harsh environments. Factors contributing to corrosion include:
- **Exposure to Moisture**: Areas with high humidity or direct exposure to water can accelerate rust formation.
- **Chemical Exposure**: Environments with high chemical exposure can lead to rapid deterioration of the steel.
To mitigate corrosion risks, it's vital to implement protective coatings and select appropriate alloys to enhance resistance.
Mechanical Properties Concerns
While S355 welded pipe is known for its strength, there can be concerns regarding its mechanical properties in specific applications. These concerns might include:
- **Fatigue Resistance**: In structures subjected to cyclic loading, the fatigue resistance of S355 may not meet the desired standards, necessitating thorough analysis during the design phase.
- **Impact Toughness**: In environments with extreme temperatures, the impact toughness of S355 can be affected, leading to brittle failure.
Addressing these concerns requires a comprehensive understanding of the material's limitations and application-specific needs.
Cost Implications
The financial aspect of working with S355 welded pipe cannot be overlooked. Challenges that may arise include:
- **Material Costs**: The cost of S355 steel can fluctuate based on market demand and availability, impacting project budgets.
- **Fabrication and Labor Costs**: Specialized skills may be needed for welding and fabrication, driving up labor costs.
- **Maintenance Costs**: Ongoing maintenance and protective measures to prevent corrosion can add to the overall expenses.
Understanding these cost implications allows for better budgeting and financial forecasting in construction projects.
Strategies to Overcome Challenges
Proper Welding Techniques
To address welding issues effectively, employing proper techniques is essential. Considerations include:
- **Preheating**: Always preheat S355 welded pipes according to the specifications for the material thickness and type of welding being performed.
- **Welding Procedures**: Develop and follow a detailed welding procedure specification (WPS) to ensure consistent and high-quality welds.
- **Post-Weld Heat Treatment (PWHT)**: Implementing PWHT can relieve stresses and improve the mechanical properties of the weld.
Material Selection
Selecting the right materials for specific applications is crucial in mitigating issues associated with S355 welded pipe. This involves:
- **Choosing Coatings**: Apply protective coatings to enhance corrosion resistance based on the environment of use.
- **Alloying Elements**: Consider using alloying elements that improve toughness and corrosion resistance when required.
Preventive Maintenance
Implementing a robust preventive maintenance program is essential for prolonging the lifespan of S355 welded constructions. Key strategies include:
- **Regular Inspections**: Conduct routine inspections to identify signs of corrosion, wear, or structural issues before they escalate.
- **Timely Repairs**: Address any identified issues promptly to maintain the structural integrity and safety of the welded pipe.
Budgeting Accurately
Accurate budgeting is vital for managing the costs associated with S355 welded pipe. This can be achieved by:
- **Detailed Cost Analysis**: Perform a thorough analysis of materials, labor, and potential maintenance expenses to create a realistic budget.
- **Contingency Planning**: Allow for contingencies in the budget to account for unforeseen challenges that may arise during the project.
Case Studies: Success in Utilizing S355 Welded Pipe
Several successful projects have demonstrated effective strategies for overcoming challenges associated with S355 welded pipe.
- **Case Study 1**: A bridge construction project utilized S355 welded pipes, implementing rigorous preheating and post-weld heat treatment that resulted in high-quality joints and minimized distortion.
- **Case Study 2**: In a petrochemical facility, a combination of advanced coatings and regular maintenance schedules significantly reduced corrosion-related downtime and extended the life of the infrastructure.
These case studies highlight how adhering to best practices can lead to successful project outcomes, even when challenges arise.
Frequently Asked Questions
1. What is S355 steel used for?
S355 steel is commonly used in construction and structural applications, including bridges, buildings, and industrial structures, due to its high strength and weldability.
2. What are the advantages of using S355 welded pipe?
The advantages include high strength, good weldability, and cost-effectiveness, making it suitable for various applications in construction and engineering.
3. How can I prevent corrosion in S355 welded pipe?
Preventing corrosion in S355 welded pipe can be achieved through protective coatings, proper material selection, and regular maintenance inspections.
4. What are the common welding techniques for S355 steel?
Common welding techniques include MIG, TIG, and MMA welding, with attention to preheating and post-weld treatments to ensure the integrity of the weld.
5. How can I address mechanical properties concerns in S355 welded pipe?
Understanding the specific application requirements and using appropriate design techniques can mitigate mechanical properties concerns, including fatigue and impact toughness.
Conclusion
Working with S355 welded pipe presents various challenges, from welding issues to corrosion resistance and cost implications. However, by understanding these challenges and implementing effective strategies, such as proper welding techniques, material selection, preventive maintenance, and accurate budgeting, we can overcome obstacles and achieve successful project outcomes. Embracing these best practices will ensure that S355 welded pipes continue to be a reliable choice in the construction and engineering sectors.
Key words:
S355 Welded Pipe
Related news